5 THINGS TO KNOW ABOUT FUEL POLISHING
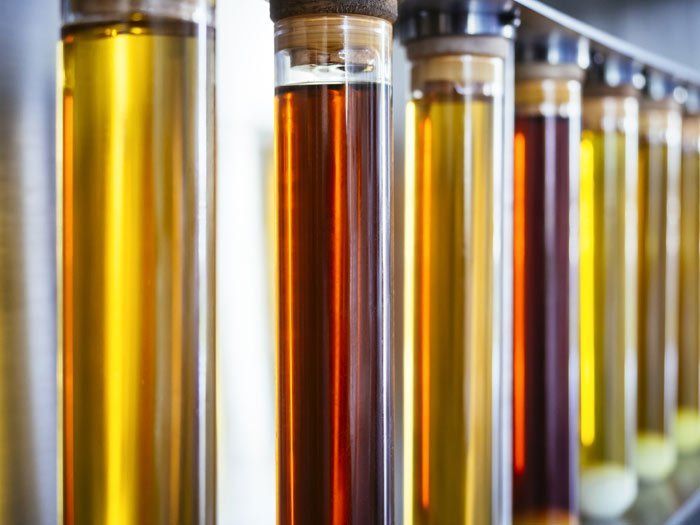
Managers and business owners in charge of industrial operations need to understand the importance of maintaining the purity of fuel to keep a facility and operation productive and effective.
Many engine failures are the result of issues that develop in the fuel tank of a mechanical system. This means that procedures such as fuel polishing are essential to maintaining mechanical systems and ensuring that they enjoy the maximum possible lifespan.
The following are five things you need to know about fuel polishing for the benefit of your industrial operation.
FUEL DEGRADATION
The purpose of fuel polishing is to protect stored fuel from degradation over time. Fuel that is stored needs to be adequately maintained over time or it will quickly succumb to problems like microbial growth and sludge buildup that will render it unusable or at least inefficient.
While you can take measures to prevent fuel degradation such as monitoring and maintaining a fuel system, fuel polishing is one of the best ways to keep stored fuel in the best possible condition over time.
OPTIMIZATION OF FUEL QUALITY
Fuel polishing involves optimizing the quality of fuel by taking contaminants like water and sludge out of it. Contaminants in fuel can lead to a lot of issues inside a mechanical system like injector failure, power loss, combustion issues, and emissions problems.
Contaminants removed during fuel polishing include a variety of different types of solids. Naturally, solids will gather in fuel that is stored in a holding tank. The fuel polishing process becomes increasingly important the longer fuel needs to be stored in a holding tank before it is combusted.
Different types of fuel can be stored for different periods of time. Be sure to check the requirements for the kind of fuel you are using.
THREE STEPS OF THE PROCESS
Before having fuel polishing performed at your facility, you should understand what the process entails. The first step is removing water that could interfere with the operation of injectors. Then, a fuel conditioner is used to stabilize stored fuel. The last step is to put a water block fine filter through the fuel that will take out any emulsified water or any solid matter.
PREVENTION OF MECHANICAL MALFUNCTIONS
The fuel polishing process offers multiple benefits, but one of the most significant is that fuel polishing prevents malfunctions in mechanical systems.
Faulty fuel can be hard on an engine and lead to premature wear and tear on engine parts. Contaminated fuel means that a mechanical system's components will operate less efficiently and will need to put in more effort to get the same amount of work done.
Fuel polishing can generally improve the bottom line of an industrial operation by keeping maintenance costs for parts down while also maximizing the lifespan of engines and generators. In fact, statistics show that over
70 percent of all generator failures are caused by fuel issues that could be avoiding through fuel polishing.
CLEANLINESS OF EXHAUSTEvery engine will give off exhaust. Low quality fuel or fuel that is contaminated will burn and give off more heavily polluted exhaust. Fuel polishing is good for the environment because it leads to cleaner burning fuel.
Also, the efficiency benefits offered by fuel polishing make it so that industrial operations can maintain productivity while consuming smaller amounts of fuel. If fuel becomes excessively degraded over time, it will need to be disposed of and cannot be used. Disposing of fuel can be harmful to the environment.
If you're interested in learning more about how fuel polishing can improve your industrial operation, contact
Paul Murray Oil, Inc. with your questions and inquiries.